Materials technology
- Home
- MATERIALS TECHNOLOGY
- Decoration
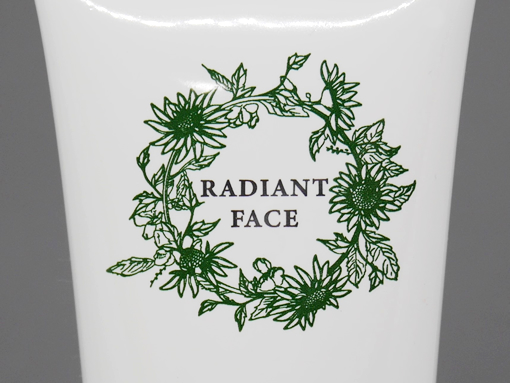
Cosmetic Tube Decoration
Offset printing, screen printing, and hot stamping are three prominent techniques used for tube decoration, each offering unique advantages that cater to different branding needs and aesthetic preferences.Offset Printing is renowned for its ability to produce high-quality, detailed images and vibrant colors, making it an ideal choice for large production runs. This method excels in delivering consistent results across various substrates, allowing for intricate designs and multi-color prints that are well-suited for product branding. Its efficiency and cost-effectiveness make it a popular option for brands looking to achieve professional-quality packaging at scale.
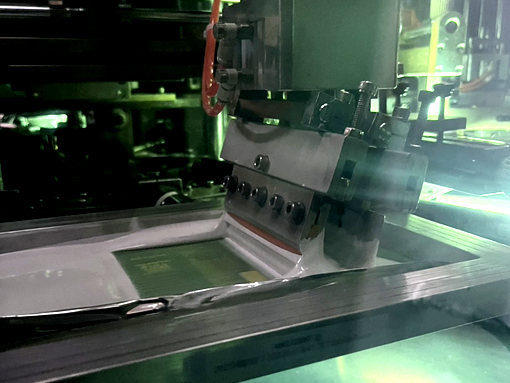
Screen Printing
Screen Printing stands out for its versatility and tactile quality. This technique is particularly effective on irregular surfaces, enabling bold graphics and vibrant colors to be applied directly to the tube material. Screen printing allows for the use of specialty inks, such as metallics and fluorescents, providing a unique visual appeal that can enhance brand recognition. It is suitable for both small and large production runs, making it a flexible choice for various applications.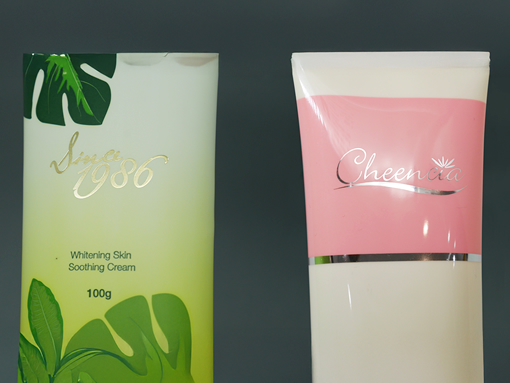
Hot Stamping
Hot Stamping adds a touch of luxury and sophistication to tube, eye-catching designs. This technique employs a heated die to transfer metallic or glossy foils onto the surface of the tube, resulting in striking finishes that are resistant to wear and fading. Hot stamping is often used for branding elements such as logos and text, helping products stand out in a competitive market and conveying a sense of exclusivity.Together, these printing technologies offer a range of options for tube decoration, allowing brands to choose the method that best aligns with their visual identity and marketing goals.